SERVICIOS
Inspección Radiográfica
La radiografía industrial es un método de inspección en Ensayos No Destructivos que utiliza radiaciones gamma para verificar la condición o estructura interna de una pieza o componente de diversos materiales que son registradas en una película radiográfica o pantalla fluorescente obteniéndose una imagen permanente.
La radiografía se utiliza para examinar una gran variedad de productos metálicos y no metálicos, determinando la sanidad interna sin dañar el producto y asegurando el uso satisfactorio de este o en su caso detectando discontinuidades o defectos como:
- Inclusiones de tungsteno o escoria
- Falta o exceso de penetración
- Concavidad en la raíz
- Falta de fusión
- Desalineamiento
- Porosidad
- Socavado
- Quemadas
- Roturas
- Corona baja
Los estándares más utilizados en este tipo de prueba son: ASME Sección V, AWS D1.1, AWS D1.5, API 1104, ASME A388, ASME A435, entre otros muchos.
Inspección de Ultrasonido (Detector de Fallas)
Permiten detectar discontinuidades superficiales, subsuperficiales e internas, dependiendo del tipo de palpador utilizado y de las frecuencias que se seleccionen dentro de un rango que va desde 0.25 hasta 25 MHz.
Las ondas ultrasónicas son generadas por un cristal o un cerámico pieza eléctrico denominado transductor y que tiene la propiedad de transformar la energía eléctrica en energía mecánica y viceversa. Al ser excitado eléctricamente el transductor vibra a altas frecuencias
generando ultrasonido.
Las vibraciones generadas son recibidas por el material que se va a inspeccionar, y durante el trayecto la intensidad de la energía sónica se atenúa exponencialmente con la distancia del recorrido. Al alcanzar la frontera del material, el haz sónico es reflejado, y se recibe el eco por otro (o el mismo) transductor.
Los estándares más utilizados en este tipo de prueba son: ASME Sección V, AWS D1.1, AWS D1.5, API 1104, ASME A388, ASME A435, entre otros muchos.
Inspección de Ultrasonido (Medición Espesores)
La técnica de medición de espesores optimiza el efecto de resonancia de las ondas para conseguir mediciones precisas de espesor de pared en tuberías, tanques, etc.
Permite la detección de pérdidas de espesor producidas por fenómenos degradatorios como erosión, corrosión, Flow Acelerated Corrosion (FAC), etc.
Medición de espesores. Para comprobar erosiones o desgastes, vigilar envejecimientos, etc.
Insp. de Partículas Magnéticas (Visibles y Fluorescentes)
Es aplicable únicamente para inspección de materiales con propiedades ferromagnéticas, ya que se utiliza fundamentalmente el flujo magnético dentro de la pieza, para la detección de discontinuidades.
Mediante este ensayo se puede lograr la detección de defectos superficiales y subsuperficiales (hasta 3 mm debajo de
la superficie del material).
La aplicación de Partículas Magnéticas consiste básicamente en magnetizar la pieza a inspeccionar, aplicar las partículas
magnéticas (polvo fino de limaduras de hierro) y evaluar las indicaciones producidas por la agrupación de las partículas en ciertos puntos. Este proceso varía según los materiales que se usen, los defectos a buscar y las condiciones físicas del objeto de inspección.
Para realizar la inspección por Partículas Magnéticas existen varios tipos de materiales que se pueden seleccionar según la sensibilidad deseada, las condiciones ambientales y los defectos que se requieren encontrar. Las partículas magnéticas pueden ser:
- Secas ( Fluorescentes / Visibles (varios colores))
- Visibles (varios colores)
Los Estándares más utilizados para esta prueba son: ASTM E709, ASME Sección V, AWS.
Inspección con Líquidos Penetrantes
Es un método de inspección no destructiva que detecta discontinuidades o defectos abiertos a la superficie de los materiales.
Se usa generalmente en piezas soldadas, piezas de fundición, forjas, recipientes, etc.
La prueba consiste en la aplicación de un líquido que penetra en los poros o grietas de los materiales.
Posteriormente se aplica un líquido revelador que resalta la presencia de los poros y grietas para determinar forma y tamaño de las indicaciones o defectos los cuales se analizan posteriormente por técnicos especializados.
Los Estándares más utilizados para esta prueba son: ASME Sección V, ASME E-165, AWS D1.1 entre otros.
Inspección de Caja de Vacío
Método normado para verificar la sanidad en cordones de soldadura de unión fondo-envolvente interno la cual es una práctica muy eficaz ya que garantiza mayor efectividad en la detección de fallas.
Estas zonas son críticas debido a que es donde se concentran todos los residuos del fondo y tienden a tener mayor corrosión.
Por lo anterior sugerimos realizar la prueba con caja de vacío ya que nos garantiza no tener fugas en soldaduras en la operación de cualquier tanque de almacenamiento.
Inspección Visual
Es un método de inspección no destructivo aplicado principalmente a soldaduras para verificar que su integridad mecánica cumple con las especificaciones o estándares.
Esta técnica, siempre se realiza como fase previa a otros Ensayos más sofisticados. Facilita el trabajo posterior y establece la secuencia de trabajo.
Es por tanto el más empleado por su sencillez, rapidez y economía de aplicación.
Procedimiento:
* Iluminar el objeto a inspeccionar con luz.
* Inspeccionar bien por:
1.-Visión ocular directa
2.- Visión ocular utilizando medios auxiliares (lupas,
microscopios, fibras ópticas, endoscopios etc.)
3.-Medios artificiales (células o captadores fotoeléctricos)
Los estándares más comunes utilizados en este tipo de servicios son: ASME Secc. V, AWS D1.5, AWS D1.1.
Pruebas Hidrostáticas y Hermeticidad
Es la aplicación de una presión a un equipo o línea de tuberías fuera de operación, con el fin de verificar la hermeticidad de los
accesorios bridados y la soldadura, utilizando como elemento principal el agua o en su defecto un fluido no corrosivo.
Todo equipo nuevo debe ser sometido a una prueba de presión (hidráulica), en los talleres o de la misma forma se realiza en campo en caso de una construcción, o proyecto industrial.
La prueba hidrostática también aplica cuando se reemplaza o se reparan líneas existentes.
La prueba hidrostática nos permite:
– Determinar la calidad de la ejecución del trabajo de fabricación o reparación de la línea o equipo.
– Comprobar las condiciones de operación para garantizar la seguridad tanto de las personas como de las instalaciones.
– Detectar fugas.
Pruebas Neumáticas
La prueba neumática es un procedimiento que utiliza la presión del aire (Nitrógeno) para testear fugas en las tuberías; además
de limpiarlas y secarlas, permitiendo que misma quede lista al final del testeo.
La prueba neumática se utiliza cuando otros métodos no son factibles; por ejemplo en caso de muy bajas temperaturas, el testeo con agua se ve imposibilitado.
Las pruebas neumáticas se utiliza cuando otros métodos no son factibles; por ejemplo, en caso de congelamiento, el testeo con agua se ve imposibilitado y una prueba neumática permite el ensayo en éstas condiciones.
Análisis de Metalografía
La metalografía es el estudio de la microestructura de todos los tipos
de aleaciones metálicas. Puede definirse con más precisión como la disciplina científica de observar y determinar la estructura química y atómica y la distribución espacial de los constituyentes, inclusiones o fases en aleaciones metálicas.
El análisis de la microestructura de un material ayuda a determinar si el material se ha procesado correctamente.
Los pasos básicos para un examen metalográfico adecuado incluyen:
toma de muestras, preparación de muestras (corte y corte, montaje,
esmerilado plano, pulido en bruto y final, grabado), observación microscópica, imágenes digitales y documentación, y extracción de datos cuantitativos a través de métodos estereológicos o de análisis de
imágenes.
Inspección de Identificación Positiva de Materiales (PMI)
La Identificación Positiva de Materiales (PMI) le ayuda a determinar la
composición química de materiales e identificar el tipo de aleación con la
que están compuestos materiales tales como tubos, válvulas, bombas, etc.
La Identificación Positiva de Materiales (PMI) le ayuda a verificar que los
componentes que conforman los distintos materiales corresponden con sus
requerimientos.
Estos equipos tiene capacidad para detectar elementos tales como: Ti, V,
Cr, Mn, Fe, Co, Ni, Cu, Zn, Zr, Nb, Mo, Hf, TA, W, Re, Pb, BI, Pd, Ag,
Sn.
Ventajas de la Identificación Positiva de Materiales (PMI):
No daña los materiales y componentes ya que es un Ensayo No
Destructivo (END).
Aporta resultados rápidos y fiables.
Prueba de Boroscopia
Las inspecciones boroscópicas son inspecciones visuales en lugares inaccesibles para el ojo humano con la ayuda de un equipo óptico, el boroscopio.
En el interior de este tubo hay un sistema telescópico con numerosas lentes, que aportan una gran definición a la
imagen.
El boroscopio es sin duda una de las herramientas imprescindibles para trabajos de inspección en las partes internas de determinadas máquinas sin realizar grandes desmontajes.
Se utiliza ampliamente para la observación de las partes internas de motores térmicos (motores alternativos de combustión interna, turbinas de gas y turbinas de vapor), y para observar determinadas partes de calderas, como haces tubulares o domos.
Ensayo de Dureza
Los ensayos de dureza están basados en la aplicación de una carga fija a un muescador sobre la superficie lisa de la muestra, lo que ayuda a medir la profundidad de la
penetración, indicando de esta forma la resistencia a la carga.
Los ensayos de dureza están normalmente categorizados dentro de los ensayos no destructivos ya que su realización no implica la destrucción de la muestra, lo
que permite el uso del material para su cometido final sin necesidad de ser reemplazado.
Floor Scanner
Aplicaciones Tecnológicas
Evaluación de espesores y corrosión por escaneo computarizado digital a tanques, tuberías y Recipientes a presión
(LFET).
Nuestra Experiencia
■ Inspección Radiográfica (Licencia de Operación Núm. A00.200/0121/2020)
■ Inspección de Ultrasonido (Detector de Fallas)
■ Inspección con Ultrasonido (Haz Recto)
■ Inspección de Ultrasonido (Medición de Espesores a placas, tuberías y equipos)
■ Inspección con Partículas Magnéticas (Visibles y Fluorescentes)
■ Inspección con Líquidos Penetrantes (Visibles y Fluorescentes)
■ Inspección Caja de Vacío
■ Pruebas Hidrostáticas y Neumáticas (Atestiguamiento y Realización)
■ Análisis de Metalografía
■ Inspección de Identificación Positiva de Materiales (PMI)
■ Pruebas de Boroscopìa
■ Análisis de Falla
■ Análisis Químico de Aleaciones en Laboratorio fijo.
■ Ensayos de Dureza
■ Inspección Visual
■ Calificación de Habilidad de Soldadores
■ Elaboración y Calificación de Procedimiento de Soldadura
■ Supervisión en trabajos de construcción en talleres a equipos revisión de materiales, planos dimensiones e inspección.
■ Cursos en Ensayos No Destructivos con certificado ante ASNT en sitio o en Instalaciones en Nanchital, Ver.
■ Consultorías en materiales, códigos y normas de construcción y mantenimiento en equipos estáticos
■ Floor Scaner (Inspección de placas de fondos en tanques).
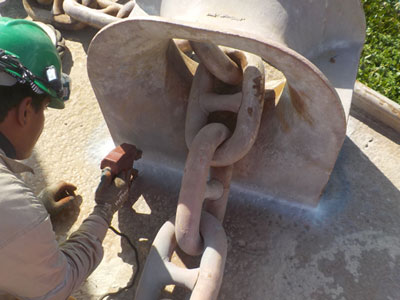
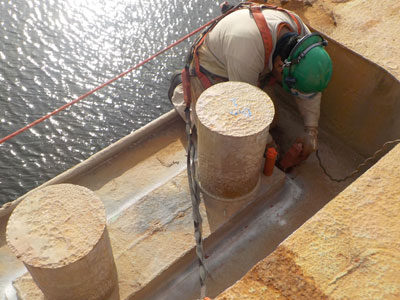
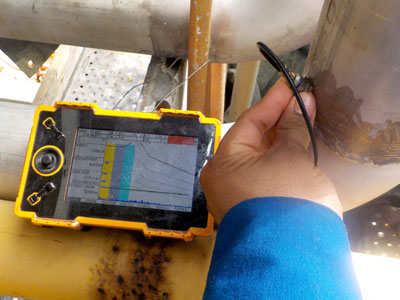
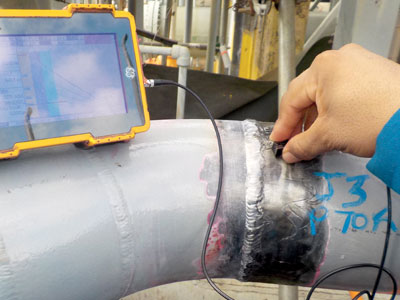
Nuestro equipo de trabajo está capacitado y con los principios de compromiso, profesionalismo, confidencialidad, integridad, garantizando confianza en los resultados emitidos de nuestros clientes.